For traditional gear motor driving system softgel encapsulation machine, softgel die rollers installation and alignment and medicine injection timing adjustment are very important and critical steps during softgel machine production process. The correctness of these adjusting processes directly affects the quality of the soft capsules, such as leakage, seam rate, and the appearance of the capsule shape. So here are some practical tips for you.
1. Softgel Machine Die Roller Set Installation:
Loosen the handwheel that holds the die rollers on the left side of the softgel encapsulation machine (facing the operating surface), loosen the handwheel that fixes the die rollers, then loosen and remove the fastening handwheels on the left and right sides of the door beam, and place them on the platform for later use. Pull out the pin rod on the left side of the door beam and put it aside, pull out the door beam horizontally with both hands Take out the mold marked with “R” on the end surface from the mold box, and install it on the mold seat of the right main shaft with the non-marked end facing inward. Install the door beam according to the reverse operation of removing the door beam, turn the mold seat of the fixed mold, the pin enters the pin hole of the mold, tighten the right hand wheel of the fixed mold, and tighten the left hand wheel of the fixed mold in the same way.
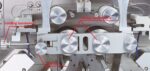
2. Softgel Die Rollers Aligment
Open the lid behind the soft gelatin machine head and check the die roller adjusting device. Loose bolt 1, bolt 2, bolt 3 and bolt 4. Observe from front of the softgel machine and adjust bolt 3 or bolt 4 on back at the same time, to make one groove on left die roller align with one groove on right die roller and then use our special made die roller alignment tooling to check if the alignment is good.
When die roller alignment is good, face to the front of the soft gel encapsulation machine and Insert a piece of tissue paper suitable for the length of the die rollers into the middle of the left and right molds, and tighten the die roller holding handwheel until the tissue paper does not fall off. tighten bolt 1, bolt 2, bolt 3 and bolt 4. Then loose the die roller holding handwheel to separate the two die rollers.
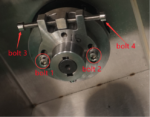
3. Medicine Pump Injection Timing Adjustment
Install the injection wedge(segment) and distribution plate(guiding plate)on to the switch plate.
Remove the left and right covers of the feed pump and check the records of assembling the pump assembly. It is now assumed that the material is fed from the right side of the feed plate and the first hole of the plunger is discharged (facing the operator). When the main engine is running, when the feed pump runs to the extreme left position, turn on the pneumatic switch to fix the feed pump at the extreme left position. Stop the main machine, place two sheets of thin paper between the two molds, then start the elevator to lower the syringe to the injection position, and observe the position of the mold line and the injection line. Click the “Electric” button on the host to make the mold index line and the syringe index line form a (︹) shape. Turn off the pneumatic switch, engage the synchronization gear, and complete the synchronization adjustment. Cover the left and right covers of the feed pump, add a small amount of liquid paraffin oil into the liquid hopper, set the machine speed to 1 rpm, start the machine, close the switch lever of the syringe switch plate, and check the liquid injection status, if it is abnormal , that is, shutdown inspection.
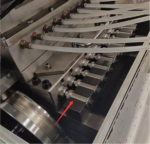
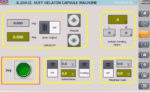
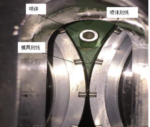
Until now, all the die roller alignment and injection timing process are done. During the softgel production process, if the capsule sealing was not good or there was leaking problem, please don’t forget to observe the die roller alignment and timing again to check if they are correct!
You can refer to the following video for more vivid process