1. Servo Motor Driving System
Totally 4 servo motors are used on our JL-250III softgel machine: 2 for the softgel die roller main axis, 1 for the medicine pump plungers and 1 for the medicine pump reversing plate.
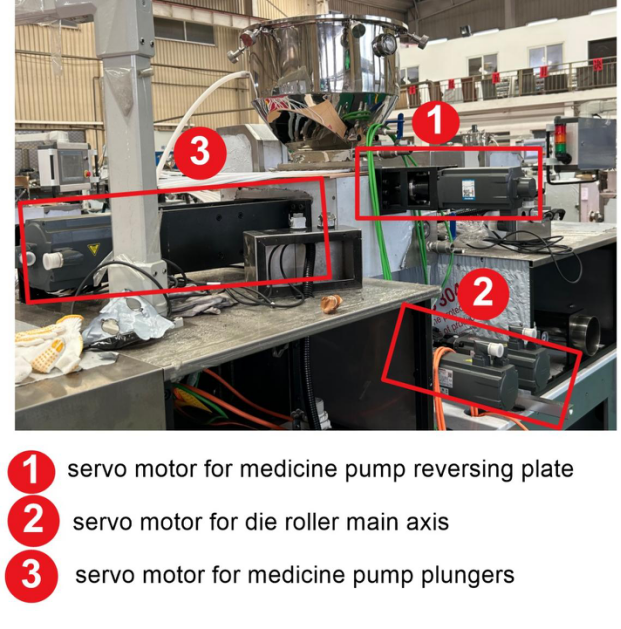
① Servo motor for softgel machine medicine pump reversing plate
So the operator just need to press the button on the PLC touch screen and the pump injection timing can be adjusted automatically
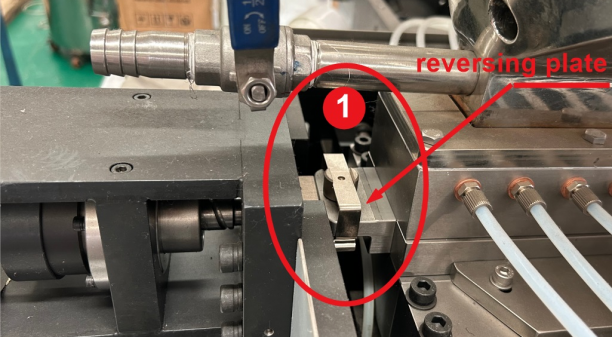
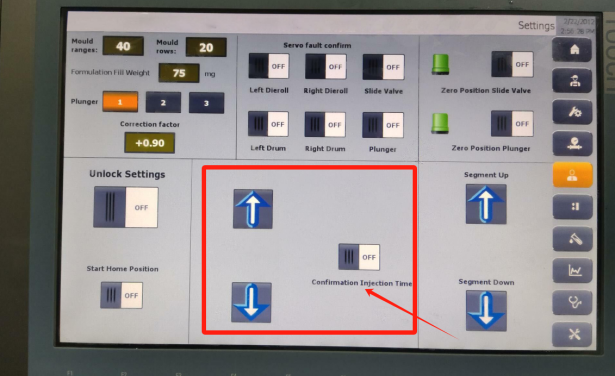
② Servo motor for die roller main axis:
1 servo motor for each main axis. So
a. Vibrations caused by traditional gear transmission are greatly reduced, and the soft gelatin machine can run faster and more stable, the highest running speed can be 8RPM and regular running speed can be 5~6RPM, which will increase production capacity dramatically
b. The softgel die roller alignment can be done automatically, no need adjust manually.
c. The operator can monitor alignment in real time, once the die roller alignment is not good, the machine can detect immediately and shut down automatically, so that to protect the die rollers.
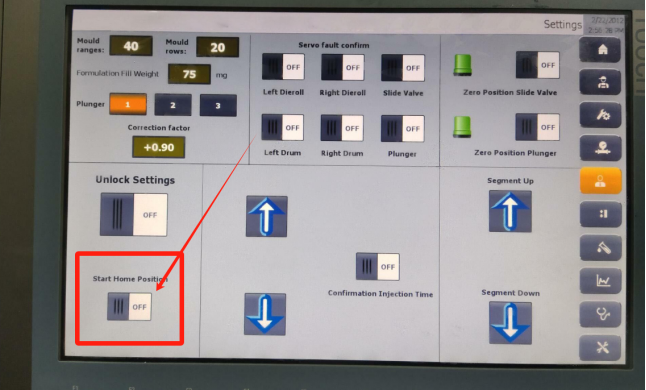
③ Servo motor for gelatin machine medicine pump plungers
Instead of using a gear to drive a cam connected to the softgel encapsulation machine medicine pump, we adopted a servo motor to drive the reversing plate directly, so that
a. The filling volume adjusting is more accurate
b. And more importantly, the filling volume can be adjusted automatically, and the operator just need to input the target filling volume on the PLC touch screen.
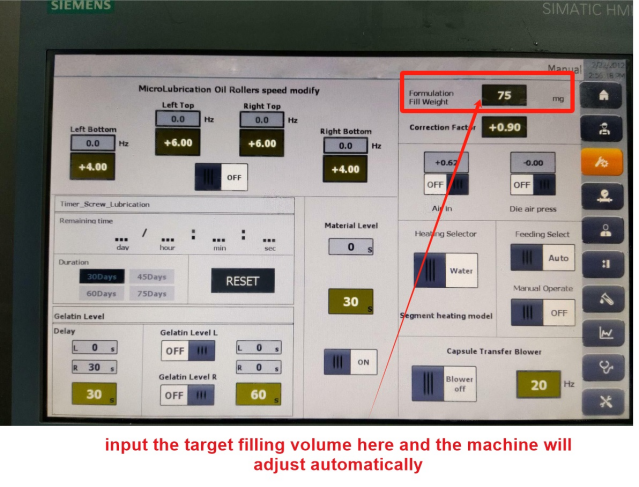
2. Automatic Gelatin Thickness Adjusting System(AGT system)
This System is consist of four physical sensors(two on each side) and two lifting motors installed on the spreader boxes(one on each side)
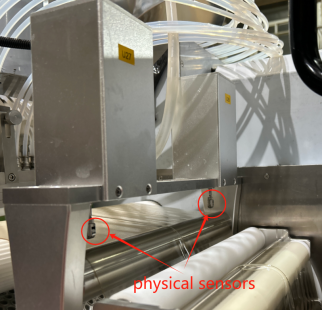
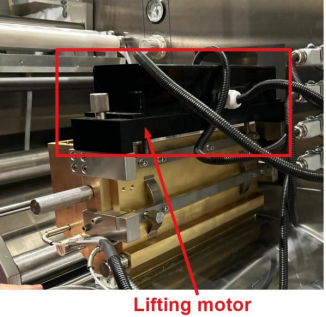
a. Physical sensors have higher sensitivity and most importantly, compared with laser sensors(like adopted by CHANGSUNG and SKY), physical sensors have very good performance on both transparent gelatin film as well as color gelatin film
b. Using cooper spreader boxes instead of stainless steel(adoped by CHANGSUNG and SKY), with better thermal conductivity and more uniform temperatures
c. The operator just need to input the target film thickness on touch screen and the gelatin film thickness can be adjusted automatically, which saves raw material and production time a lot.
d. The accuracy will not exceed±0.02mm.
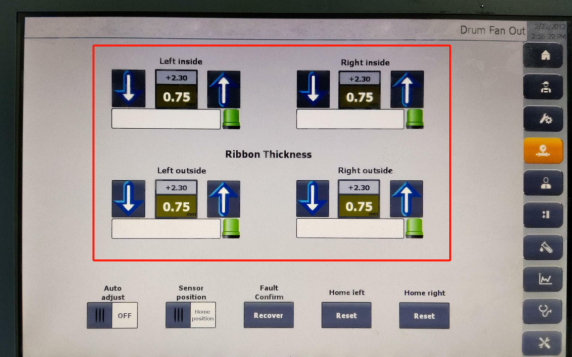
3. Micro Lubrication System
We use precision metering oil pump for the lubricating system. And the operator just need to input the target oil flow on the PLC touch screen and the the oil volume can be adjusted automatically and precisely controlled. We realized truly “micro lubricating” for the gelatin ribbon, and capsules need no more cleaning or polishing after totally drying.
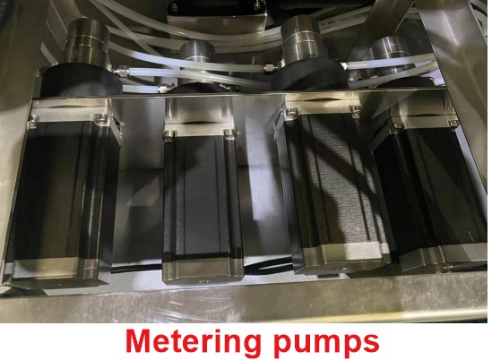
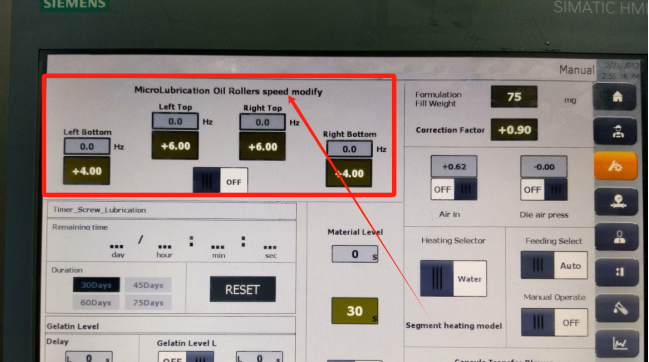
4. Water Heating System
① Die roller wedge:
We adopt hot water circulation heating for the die roller segment, so the temperature can be more accurate and stable.
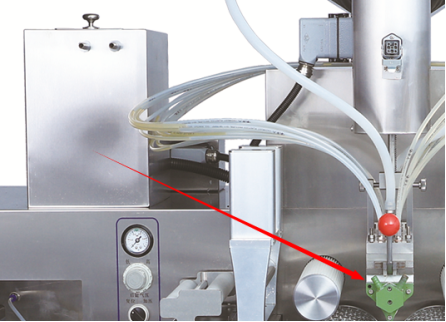
② Medicine Hopper:
a. The hopper is rounded style and the internal welds have been carefully processed and there are no sanitary dead corners.
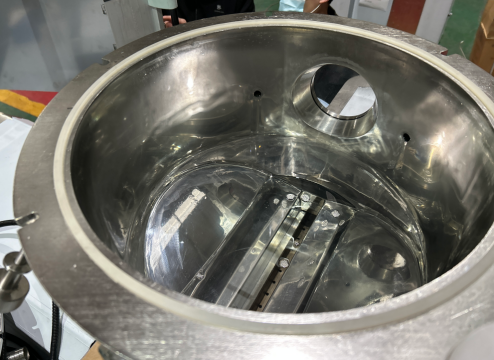
b. There is a heating layer on the medicine hopper filled with water or oil(depends on clients’ material), and hot water heating makes the medicine inside the hopper temperature even and better fluidity.
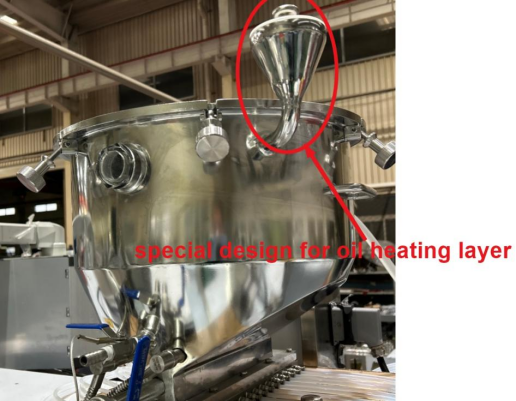
c. The hopper was designed closed style with C clamp, so that the manufacturers can close it and fill Nitrogen when the filling material is fish oil or other material easy to be oxidized.
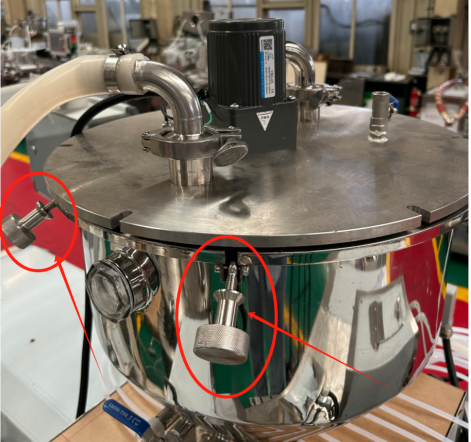
5. Casting Drum System
a. We adopted Japanese NSK axis for the casting drums, which is same axis we used for the die roller main axis.
b. Different from what most of the softgel machine manufacturers do–putting the air blowers under the casting drums, we installed big stronger air blower fans behind the casting drums and designed a special curve air tunnel to get much better cooling effect.
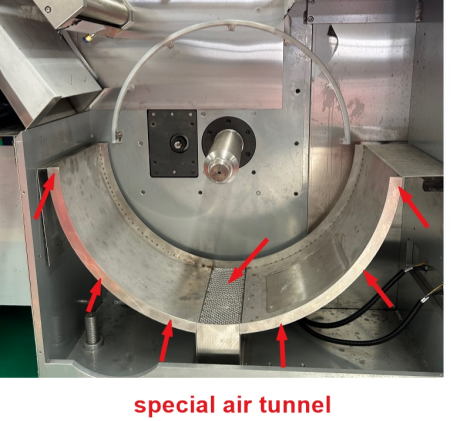
c. The surface of the casting drums is processed well and the circle jump of the casting drum is less than 0.05mm
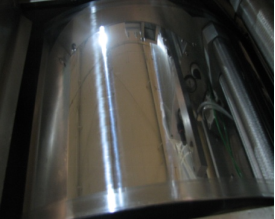
6. Electrical Components&HMI
a. All the electrical components and HMI are Siemens or ABB brand
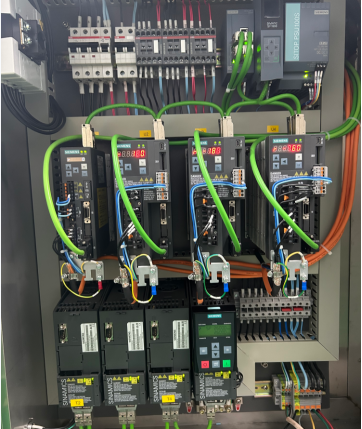
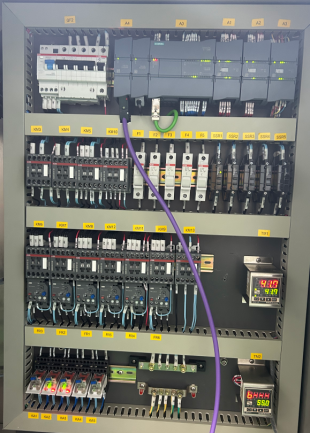
b. HMI Easy to learn and operate
c. 21CFR part 11 compliance
d. Modification of software is available
e. The whole softgel production process can be monitored