The decision to launch a soft gel production company might be nerve-racking. Despite the enormous soft gel sector, only some businesses can make soft gel capsules of high quality. Most people are unaware that the machinery and components used in a manufacturer’s production line are crucial to that company’s performance in producing soft gel capsules.
If you want to equip your production line for success, you’ve come to the right place. In this comprehensive guide, we’ll walk you through the key components and machinery you need to ensure a seamless and effective operation.
Which Machines Are Important for Soft Gel Production?
Wuxi Jangli Company more professional softgel machine supplier
A successful soft gel production line needs various machines and components. To obtain high-quality soft gel capsules, you must follow specific procedures and use appropriate equipment during each stage of the production process. Whichever soft gel capsules you manufacture will require the following machines and components.
Gelatin and Medicine Preparation System
The preparation of gelatin and filling medicine is the initial stage in creating soft gels. The melting of gelatin and preparation of filling medicine involves various machines and components. We highlight them as follows:
Gelatin melting tanks(Gelatin Reactor):
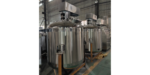
Gelatin raw materials are stored and transported in the form of granules. To encapsulate soft capsules, solid granule gelatin needs to be melted into gelatin glue(solution), and then made into rubber(gelatin film) before it can be used on soft gel encapsulation machine. The gelatin melting tank is the equipment that needs to be used to prepare the gelatin liquid. This tank is a three-layer structure with mixing stirrer, the inner layer is used for reacting, the jacket layer is used for circulating hot water to heat the tank, and the outermost insulation layer is used for filling insulation materials (usually rock wool ) to insulate the tank. The inner layer of the tank can withstand a certain positive and negative pressure. The negative pressure is used to eliminate the air bubbles in the gelatin solution to ensure the quality of the liquid gelatin. The positive pressure is used to discharge the melted gelatin. During the gelatin preparation process, continuous stirring is required to ensure the uniform mixing of liquid gelatin.
Gelatin Service Tanks
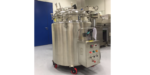
Before feeding gelatin to the soft gel encapsulation machine, the tanks assist in maintaining it uniform at an ideal temperature. There are three layers in this crucial tank: one inside the tank, one at the heating jacket, and a third at the outer insulation cladding. This tank can bear some positive pressure, so that to transport gelatin liquid to soft gelatin capsule machine gelatin spreader boxes.
Medicine Mixing tanks
Melted gelatin mixes with additional ingredients in the tank to create a soft gel composition. Other active substances include excipients, additives, colors, and flavors. A consistent and uniform soft gel mixture forms after mixing all the ingredients.
Vacuum systems
The vacuum systems control the flow, remove any excess air or gas in the gelatin mixture and eliminate air bubbles. Vacuum System often consists of a set of vacuum pump and a vacuum condenser to collect bubbles and protect the vacuum pump.
Heating and cooling systems
The temperature of different parts and stages of the encapsulation process is controlled and maintained with the aid of the systems. The gelatin in the melting tank first warms before melting. The systems aid in preserving the ideal temperature for shell formation after the gelatin melts and mixes with the other ingredients.
The proper flow and homogeneous filling of the encapsulation cavities are made possible by maintaining the viscosity of the gelatin material. The drying chambers or tunnels receive cool air from the cooling systems. It facilitates drying while stabilizing the capsules’ structure by lowering their temperature.
Gelatin filtration systems
The impurities (particulate matter, pollutants, dirt, and others) in the gelatin solution are removed by the filtering systems using membrane or depth filtration. The systems enhance the optical clarity of the gelatin solution and avoid the formation of off-tastes by eliminating the contaminants.
The systems regulate the gelatin solution’s consistency and viscosity. The systems also protect against clogging and equipment blockages that the contaminants would have brought on.
Agitators and mixers
Gelatin is mixed with other ingredients. When the ingredients are put into the mixing or melting tank, the agitators and mixers ensure that everything is thoroughly mixed, resulting in a consistent and homogenous gelatin mixture.
The gelatin mixture is constantly in motion thanks to the agitators and mixers, which prevent heavier components from settling to the bottom.
Formulation and blending machine
The formulation and blending machines in the soft gel production line do the accurate formulation and thorough mixing of gelatin and other ingredients to create a consistent soft gel mixture.
The table below outlines the two pieces of equipment and their uses:
Equipment type(formulation and blending) | Uses |
Ingredient weighing and measuring | -Helps to measure the component quantities needed for the gelatin mixture accurately. In this manner, the soft gel mixture’s consistency is maintained between batches. |
-Allows for simple scalability based on the required production volume. | |
-Minimizes measurement-related human error. | |
-Helps with accurate record-keeping as correct quantities are dispersed. | |
Homogenizers | -Splits bigger particles into smaller ones for improved shell formation. |
-Aids to uniformly distribute ingredients with limited solubility or those oil-based throughout the gelatin mixture. | |
-The emulsions in the gelatin mixture are stable. | |
-It improves the texture and appearance of the gelatin mixture, creating soft gel capsules that look nicer. | |
-Preserves the gelatin mixture’s content consistency from batch to batch. |
Soft gel encapsulation equipment
These are the specialist equipment and components made especially for soft gel encapsulation. The machines and components are listed below.
- Soft gel encapsulation machines
- Gelatin supply systems
- Drying tunnels or chambers
- Cooling systems
- Soft gel drying and polishing machines
Soft gel encapsulation equipment use
- They accurately pour gelatin material into the molds and cavities used for encapsulation. As a result, the gelatin that forms the soft gel capsules’ outer shell is evenly distributed.
- The equipment then enables the precise filling of the gelatin mixture into the encapsulation cavities. Ensuring all ingredients distribute evenly inside the soft gel capsules.
- It uses the gelatin mixture and molds to form soft gel capsule shells. The equipment uses regulated heating and cooling to build and solidify the gelatin—as a result, consistent, smooth, appropriately shaped soft gel capsules form.
- The soft gel drying system makes drying, removing extra moisture, and hardening the gelatin shells easier. Therefore increasing the shelf life of the capsules guarantees their stability while preserving their structure.
- Quality control mechanisms are frequently incorporated into soft gel encapsulating machines to monitor different variables, including shell thickness, weight, and aesthetic appeal. The controls aid in rejecting capsules that don’t adhere to the desired quality standards.
- The automated elements of the machine are intended to make the encapsulation process more efficient. Consequently, the machine lowers the number of errors and requires less human labor, increasing manufacturing efficiency.
- The machine for soft gel encapsulation has features that make maintenance and cleaning easier. As a result, the machinery continues to operate at peak efficiency, extending its lifespan and enabling quick changeovers between formulations and batches.
Quality control and testing equipment
You’ll need a quality control and testing machine in the soft gel production process. The machine is responsible for inspecting and confirming the compliance and quality of the manufactured soft gel capsules. The various machines are as follows:
- Physical property testing equipment: It is used to visually check the soft gel capsules for flaws, including dents, cracks, or irregular shapes. The result guarantees the capsules comply with the required physical and aesthetic standards.
- Gelatin bloom strength testers: They aid in determining the gelatin’s bloom strength or capacity to gel or solidify when exposed to specific conditions. They contribute to maintaining consistent gelatin quality from batch to batch in this way. If there are variances in the gel’s strength, you, as the manufacturer, can take corrective action.
- Moisture analyzers: They measure the moisture in the soft gel capsules. Excessive moisture can result in degradation, a shorter shelf life, and potential microbiological growth. Capsules may become brittle and hard if there is not enough moisture present. The production operators can monitor the moisture levels at various stages to ensure the capsules are within the desired range.
- Microbial testing equipment: The equipment aids in detecting microorganisms such as mold, bacteria, and yeast in the soft gel capsules. Testing ensures that you only produce microbially uncontaminated capsules.
- HPLC(High-performance Liquid Chromatography) systems for content analysis: You can use them as an analytical tool in quality assurance and testing procedures even though they are not a part of the soft gel encapsulation machinery. HPLC systems examine the identification, concentration, and purity of the active pharmaceutical ingredients (APIs) in the soft gel capsule.
They evaluate the soft gel capsules for dissolution. Dissolution testing determines how quickly and thoroughly the API dissolves from the capsules. The HPCL systems’ precise and sensitive identification of degradation products guarantees the capsule’s stability and quality for its shelf life.
Packaging machines
The production of the soft gel capsules is complete, and they are now ready for packaging. The finished soft gel capsules are packaged using the packaging machinery.
a.) Soft gel capsule inspection machines- Soft gel capsules are sorted and arranged by machines according to predetermined standards such as size, color, and shape. It makes the subsequent packaging steps simpler.
b.) Counting and filling machines: To ensure the correct capsules are contained in each packaging unit, batch control (counting machines) is necessary. The soft gel capsules are precisely dispensed into the required packaging containers using filling machines.
The filling machines use vibratory feeders, pneumatic fillers, and rotary fillers, to achieve accurate capsule placement and avoid overfilling and underfilling. High operating speeds on both machines allow for effective output rates. They can manage various soft gel capsules and work with various packaging arrangements.
c.) Printing and labeling equipment: In addition to applying product labels, expiration dates, batch codes, and other information on the packing material, the packaging equipment also incorporates labeling and printing systems. It guarantees correct product identification, regulatory compliance, and traceability.
d.) Packing and capping machines: The machine depends on the packaging you want for your soft gel capsules. The soft gel capsules can be packaged in separate blister packs using a soft gel blister packaging machine. The capsules can be packaged into bottles, strips, pouches, or sachets.
e.) Cartoning and case packing systems: The strips, bottles, pouches, or blister packs of soft gel capsules are assembled and packaged into cartons using cartoning equipment.
Utilities and infrastructure
They are the facilities and support systems required to ensure the machine’s correct operation and the success of the entire encapsulating process. Everything utilities and infrastructure perform as follows:
- Ensures the soft gel encapsulation machine has a dependable power supply, including electrical connections, backup power sources, and voltage stabilization systems.
- They offer the necessary water connections, temperature control devices, and filtration systems to address the machine’s water needs.
- Compressed air sources, filtration, pressure regulation, and distribution systems must be in place to adequately guarantee the system’s availability and operation of compressed air. For pneumatic systems, valves, and actuators, compressed air is necessary.
- Systems for ventilation and exhaust to get rid of pollutants in the air..
- Waste created during the encapsulation process, whether solid, liquid, or hazardous, must be handled and disposed of via waste management systems.
- To ensure a secure working environment for operators, they contain safety features, including emergency lighting, fire detection and suppression systems, and security systems. They also protect the building, the equipment, and the products from potential risk.
- They ensure that regulatory compliance standards, such as adherence to building codes and electrical and water safety standards, are met.
Regulatory compliance and documentation
The two play a significant role in the soft gel encapsulation to ensure that, as a manufacturer, you comply with relevant regulations and maintain proper records.
Regulatory compliance and documentation | |
Standard operating procedures(SOPs) | -Offer detailed instructions on how to use the soft gel encapsulation device. |
-Act as valuable guides for new hires and operators. | |
– Define the vital factors (temperature, time, pressure, and speed) for consistent soft gel encapsulation. | |
-Include safety rules, precautions, and error prevention tactics. | |
-Check that the machine operates per all applicable regulations, such as Good Manufacturing Practices (GMP), quality control requirements, etc. | |
Batch records | -Offer a thorough accounting of each batch of soft gel capsules produced. |
-Act as a source of information for quality control and traceability. | |
-Assist in ensuring that products satisfy the desired quality standards and serve as proof of quality control methods. | |
-They offer the supporting documentation required to show compliance with GMP standards and regulatory regulations. | |
-Batch recordings are valuable tools for troubleshooting and continuous improvement. | |
Electronic batch records | -Reduce the dependency on paper-based records by collecting and storing numerous data points during encapsulation, such as batch details, machine settings, and raw material utilization. |
-Real-time monitoring of critical control points and process parameters. Aids in quickly identifying irregularities. | |
-Offers a complete audit trail of all steps taken throughout the encapsulation process. | |
-Offers graphic representations of the encapsulation process, including charts, reports, and trends. |
Conclusion
Equipping your soft gel production line for success requires premium machines and components. There may be several manufacturers and suppliers, but only Jangli Equipment offers value for your money. Even after installing the equipment for your business, we continue offering our support.