What is Softgel Die Roller?
- Softgel machine die roller is the core component of the softgel machine; The filling material is injected into the die roller cavity through the wedge(segment) and when the filling material is injected, the die roller rotates and starts to bond the gelatin film from the bottom side. After the injection, it continues to rotate to bond the gelatin film on the upper side, thus forming a complete capsule;
- The softgel die rollers determine the shape and size of the capsules; All kinds of beautiful soft capsules with different shapes we have seen are realized by the soft capsule die roller set; According to the shape and filling volume required by the customer, the appropriate pockets are designed. Then ideal capsules can be made;
- The softgel machine has relatively high precision requirements, and the precision requirements of the die roller sets are also very high. High precision softgel die roller can ensure that the soft capsules produced are beautiful in shape, and the seams are strong and leak-proof;
- And because the materials used for softgel die rollers are relatively expensive, the processing time is relatively long, and the processing technology requirements are relatively high, resulting in a relatively high price of the softgel die roller;
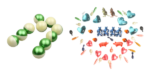
Other Names of Softgel Die Roller
- Soft gelatin capsule tooling
- Softgel tooling
- Softgel die roller set
- Tooling for soft gelatin capsule
- Softgel die rolls
- Softgel Mold
Softgel Die Roller Components and Material
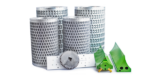
- The whole set of die roller set includes a pair of cylinders(die rollers), a injection segment(wedge), a distribution plate and a timing gear(If it was a servo motor driving softgel encapsulation machine, timing gear is not needed)
- The material of the cylinders(die rollers) is air craft aluminum; Because air aluminum is strong and lightweight and easy to be processed and after die roller processed, there will be anodizing treatment on the surface, to prevent corrosion.
- The material of the injection segment(wedge) is brass; Because brass has good thermal conductivity and after processed, there will be Teflon coating on the surface; Teflon coating is non-stick coating and can prevent gelatin film stick on the segment.
- The material of the distributing plate is PTFE and some clients prefer stainless steel material and supplier can adjust according to clients’ special requirements.
- And timing gear is only for gear driving softgel encapsulation machine; Timing gear is used to connect the die roller shaft to the main motor. For servo motor driving softgel machine, the die roller shaft is driven directly by servo motor and no need timing gear.
How Are Softgel Die Rollers Processed?
- Design and draw drawings according to the machine model and customers’ requirements, and send them to the customer for confirmation (some special capsule types require customers to provide sample capsules, send them to us for measurement, and the engineer will draw the die roller pocket size according to the measurement results of the sample capsules); For the moment we can produce matching die roller sets for most softgel machine models, including our own machines JL-100II, JL-250II, JL-250III, JL-300III, JL-150III, as well as models produced in Korea, including CHANGSUNG, SKY, Model Pharmagel made in Italy, and model made in India. . . However, there are some new machine models that we have not contacted before, so we need customers to send us sample die roller for measurement.
- After the customer has confirmed the drawings, we can purchase raw materials for processing. The raw copper rods and aluminum rods of copper and aviation-grade aluminum will be purchased, and aluminum rods of different diameters will be purchased according to the diameters of the die rollers. Then cut the aluminum rods into sections according to the length of the die rollers and the injection segment(wedge), and then the sections will be taken to the lathe for preliminary processing and grinding, and become a semi-finished die roller set.
- The semi-finished die roller will be matched with the corresponding drawings, and then taken to the CNC machining center for further processing. The drawings designed by the engineer in advance will be input into the CNC program system. The die roller pockets, positioning pin holes and end face lettering will be completed on the CNC machining center equipment. The machining time of one piece of softgel die roller cylinder in the CNC is about 20 hours. After processed in CNC center, the inside of the die roller will have a lot of burrs. After cleaning, it needs to be taken to the lathe to grind the inside, and then clean again and dried again, and the die roller cylinders are basically formed.
- The precision of the formed die roller cylinders cannot meet requirements. At this time, it needs to be further refined to improve its precision. After cylindrical grinding and end grinding, the roundness and perpendicularity of the cylinders are guaranteed. . . (Because the two important factors that determine the quality of soft capsule die roller cutting are the roundness and perpendicularity of the die roller cylinder, and only die rollers with good roundness and perpendicularity can cut neatly)
- After fine grinding, the we can do die roller surface treatment after cleaning and drying again. Our surface treatment is divided into two procedures: One is sand blowing on the surface–We use an automatic sand blower for sand blowing, which can ensure uniform sand blowing. Sand blowing can eliminate small burrs on the surface of the die roller cylinders and make the surface of the cylinders smoother; The other procedure is anodizing, because aluminum itself is relatively easy to be oxidized and corroded. , Anodizing can form a protective film on the surface of the die roller cylinders, making the die rollers corrosion-resistant and harder.
- After the anodization is completed, the entire mold processing process is basically over. The next step is our inspection process. Each of our die roller is manually inspected to ensure the accuracy of the inspection. After the inspection, the die rollers can be packed and shipped.
- The processing process of the injection segment(wedge) is similar to the die roller cylinders process, and the procedure is relatively simple, only Teflon spraying is required at the end.
Multiple Softgel Die Rollers
What is multiple Softgel Die Rollers?
- Normally there’s only one step surrounding one pocket on the die roller cylinders, but we found that the capsules can’t seal good and leak oil sometimes, we kept trying to find a way to help capsules seal better, and finally we developed multiple steps softgel die rollers.
- On multiple die roller cylinders, there is another step inside one pocket or outside the pocket or both inside and outside the pocket, and by this way the extra step(s) will help to reduce the pulling to the gelatin film and help the middle step to seal better.
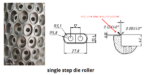
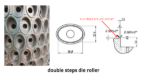
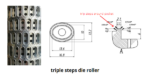
What kind of products do multiple steps die rollers suitable for?
- For common animal gelatin, when filling material is pure oil, it is easy to cut the gelatin film and capsules seam is strong and not easy to leak, so single step die roller is enough.
- For animal gelatin, when filling material is thick stuff like lecithin, double steps die rollers are recommended, because double steps can make seam stronger and not easy to leak
- Triple steps die rollers are more suitable for starch gelatin, like tapioca starch, pea starch and carrageenan. Because starch gelatin has big viscosity and gelatin film has low ductility, the capsule seam is weak and easy to leak, and triple steps die rollers can solve this problem to some extent.
What Innovations Our Company Made On Softgel Die Roller?
Our company has more than 20 years of production experience in the softgel die roller industry. Based on years of production experience, we have carried out a series of improvements and innovations on softgel die rollers.
Die Roller Outer Circle and End Face Grinding Craft
- Die roller cutting depends on supplier’s chamfering and outer circle grinding craft.
- The “concentric and positioning” outer circle grinding craft we developed has gained great praise by softgel production enterprises.
- This craft ensures the requirements on concentricity and perpendicularity of the die roller. And under regular use condition, this craft prevented unsmoothly die roller cutting effectively and prolonged the service life of the die rollers at the same time.
Triangle Blocks Between Pockets
We added triangle blocks between cavities.Die roller cutting and hexangular roller pulling gelatin ribbon can both cause gelatin ribbon deformation. Our triangle blocks and steps design on edges can reduce the passive pull of gelatin ribbon, so that reduce gelatin ribbon deformation. So our design will make seam stronger and more beautiful.
Innovations On Starch Gelatin Softgel Die Rollers
- The distance between pockets bigger: The elasticity of starch gelatin is poor, and the size of the pocket for same filling volume is larger than that of animal gelatin. By this way, after the filling material is filled, there will be enough space to prevent the seams from being squeezed by the contents and the seams are not firm.
- The arrangement of the pockets on the starch gelatin die roller should not be too dense: Compared with animal gelatin, the distance between the adjacent pockets should be increased to prevent the net gelatin from being pulled off.
- Features of the triple steps die rollers used for starch gelatin: The height of the inner and outer steps of the pocket and the height of the middle cutting step differ by 0.2 to 0.3 mm, and the height of the total step is 0.8-0.95 mm (while the height of animal gelatin is 0.4~0.5 mm. The height of the total step is 0.8-0.5 mm~0.95 mm.) After the height of the inner and outer steps changes, the starch capsules encapsulated are as shown below:
The height difference between the inner and outer steps and the cutting steps becomes smaller. So after the starch softgels are just released from the die rollers, there will be a small raised edge at the seam. Due to the large shrinkage of starch gelatin, the small edge will disappear after drying, and the seam rate is as high as 90%-100%.
- Surface sand blasting craft: In order to prevent the phenomenon of gelatin film sticking to the die rollers, the surface treatment process of the die rollers needs to be sandblasted with fine sand of more than 200 mesh, so that the anodized film on the surface of the die roller is more dense and has a frosted effect to prevent the gelatin film from sticking to the die rollers, which provides a guarantee for increasing the speed.
Our Original Conjoined Die Rollers Can Reduce Gelatin Waste and Save 20% Gelatin.
- Change arrangement mode and processing method of pockets, utilize the limited space of die roller diameter, on the premise of not changing equipment, not changing pocket size, change the distance between the pockets and increase the pocket number, increase gelatin utilization and achieve greater output.
- Take standard 20 Oblong as an example : standard die roller arrangement is 7×34=238, and the distance between two adjacent pockets is 1.25mm. Shown as in the following Picture:
- Our conjoined die roller arrangement is 7×36=252 and distance between adjacent pockets is 0.82mm. As shown in the following picture:
- Distance changed from 1.25mm to 0.82mm, which saved space and we use smaller machining tool to process the conjoined die rollers.
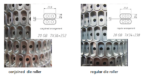
Grow Your Business With Jangli
Contact us for more details